Installing Underfloor Heating Suspended Floor Footing
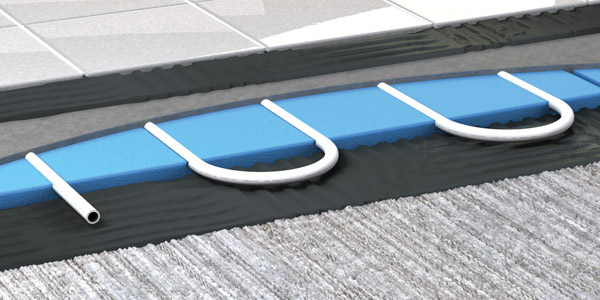
How to build a raised deck - B&Q for all your home and garden supplies and advice on all the latest DIY trends. You are about to be redirected to the following page: http://www.nhbc.co.uk/builders/productsandservices/techzone/nhbcstandards/technicalguidancedocuments/.
The Slab on Grade Installation . From a radiant heating perspective, it doesn’t matter if the slab is actually “at grade” or is poured several feet below grade as part of a full foundation. Check out our video How to Install Radiant Floor Heat Tubing in a Slab On Grade, and read this page for a full description. The fact remains that installing radiant tubing within a concrete slab is probably the easiest, most cost effective, and highest performance application of the science.
The thermal benefits are unsurpassed. Virtually any concrete pour should contain radiant tubing . After all, you may change your mind later and regret your lost opportunity. For most applications, the tubing and manifold are relatively inexpensive and the mechanical components can be installed even years later. Of course, there are always exceptions to the rule. A woodshed or an outside storage shed with a concrete floor might be a waste of tubing.
But even then you should think long and hard about the possibilities of converting these areas into heated space at some future date. I say this because often we work with people faced with the task of pouring a new slab, with tubing, over an already existing slab .
Concrete slab floors come in many forms and can be used to provide great thermal comfort and lifestyle advantages. Slabs can be on-ground, suspended, or a mix of both.
P= Exposed Perimeter of Floor (Metres) A= Area of Floor (Sq. Metres) Thermal Calculations In order to calculate how much floor insulation is needed, please refer to. How to navigate your way through the minefield that is plumbing code. A concrete vapor barrier is a sheet of polyethylene plastic (Visqueen) placed directly on top of the sub-grade before a concrete floor is poured to keep moisture from.
How much easier it would have been to install the tubing in the original slab! But, if you’re fortunate enough to be planning an original pour, the procedure is simple. In fact, the basics of a standard pour remain the same. The compacted aggregate base is first, followed by a 6 mil polyethylene vapor barrier, then insulation, then rebar or wire mesh, or both. The insulation phase is crucial for a radiant floor. Mainly, heated slabs radiate outward rather than downward, so insulation on the edges of the slab is most important.
Remember that your slab will be about 7. F. Any cooler surface in contact with the slab will try to steal its heat. If you’re pouring up against your foundation walls, insulate between the slab and the walls. For a cleaner looking installation, cut the top edge of the foam board at a 4. How you insulate under the slab depends upon the severity of your winters. In lower, warmer latitudes, the 1.
In colder regions, use 2. Heated slabs lose heat outward as well as downward. Insulating a radiant slab. Detail of insulation on a radiant slab. There are many approaches to insulating a radiant slab, but the detail at right shows a frequently used method.
Since the slab will be approximately 5 degrees warmer than the room temperature, a 7. Obviously, any cooler surface in direct contact with the slab will try to steal its heat, so a thermal break greatly reduces this heat transfer. Of course, in many situations a downward heat flow is desired as a means of creating a “heat sink” to protect the space in the event of a severe power outage or mechanical failure. A slab with such a heat sink could take days to fully cool down. Note: Many of our customers ask us about alternate slab insulation materials like radiant foils, bubble- type insulation, and thin foams of various kinds coated with vapor barriers. Admittedly, these alternate materials have two distinct advantages over “blue” or “pink” board, i.
Our opinion is based on customer feedback and our own experience. We recommend Extruded Polystyrene. So, once you’ve insulated to suit your situation, install the rebar and/or wire mesh and use rebar ties to fasten your radiant tubing to the mesh. If like most slabs you require more than one circuit of tubing, you’ll need to install a slab manifold at some convenient spot along the perimeter of the pour. The slab manifold is shipped in a plywood box that doubles as the form you pour the concrete around. Make sure the manifold box is installed plumb.
Later, when the pour is complete and you unsweat the pressure test kit from the top of the manifold, you’ll want your supply and return pipes sticking up nice and straight. Install the slab manifold very near your heat source, if possible, to keep the supply and return lines from your heat source short and easy. Depending upon which size tubing you’re using (7/8. Keep in mind that while you’re looping the tubing back and forth, up and down the slab and so forth, you won’t be trying to make a 1.
The actual bend will probably be closer to a 2. In other words, warmth equals flexibility. But whatever the temperature, just allow the tubing to conform to its natural bend. You may want to experiment with a 4 ft.
Slowly start bending until you reach the kink point. That will give you some idea of how tight your bends can be. Then later, while laying out your circuits, and after your wide, comfortable bend, you can begin spacing the tubing roughly 1. Notice the wide, comfortable bends, then the 1.
Both of these installations utilized the “heat sink” option, i. In areas prone to long power outages, this approach can give the slab a very long “thermal swing” by storing heat in the mass below the slab. Virtual Dj Djc Edition Download Cracked. Large thermal mass protects the home from freezing even after days without a heating system. Future workshop slab prepped with insulation, wire mesh, and 7/8. Come in about 6. It’s okay to cross the tubing as long as you don’t create a tubing stack so thick it threatens to rise above the surface of the slab.
You can see how that wouldn’t be a great idea! Three- loop manifold system. The three- loop system pictured here is a commonly used layout pattern for a typical slab on grade installation. Although it’s perfectly okay, and sometimes necessary, to cross one tube over another during tubing layout, notice how this simple configuration places each loop within its neighbor, starting from the outer connections of the manifold and working toward the center. Once the tubing is run, and all the connections are made to the manifold, replace the front cover of the manifold box and pressurize the system to 5. PSI. Wait several hours or overnight.
Sometimes the air in the tubing cools down and a few pounds of pressure are lost. However, if the gauge indicates more than a 5- PSI drop, check for leaks in the tubing. Most of the time, the connections to the manifold just need a bit more tightening. If that doesn’t solve the problem, inspect the tubing for signs of damage. A sharp piece of wire mesh may have punctured the tubing during installation. It’s rare, but it can happen.
If a puncture is discovered, use a repair coupling, or if that method offends your sense of perfection, replace that circuit of tubing. In most cases, replacing a complete circuit will cost less than $2.
It will cost only pennies if you can cut out the damaged section and reuse the tubing later in a floor joist application. It is also a good idea to stuff some scrap foam, newspaper, an old rag, or whatever, around the tubing where it enters the manifold box.
That way, if your concrete is unusually soupy, it won’t be able to flow into the box and touch the copper manifold. Once the system has been tested and proven free of leaks, lower the pressure to 2. PSI. With the gauge at 2.
PSI, you’ll have a visual indication that the system is holding pressure during the pour itself. Should that pressure drop, find the source of the leak and either use a repair coupling, or form around the damaged area and repair it later. Just remember that damage during the pour is rare. The tubing isn’t delicate and in most cases is spaced 1. Cara Hack Akun Facebook Melalui Email Marketing. There’s plenty of space to walk between the tubing runs. If concrete needs to be wheeled across the floor, simply lay down some plywood planks to spread out the weight and protect the tubing. And while we’re on the subject of pre- pour preparations, this would be the ideal time to install the “sensor sleeve” if a floor sensor is being used to control the zone instead of the standard wall mounted thermostat.
The “sensor sleeve”The “sensor sleeve” installed in the manifold box. Briefly, a floor sensor is a small thermistor that monitors the actual floor temperature instead of the air temperature in the zone heated by the slab. It’s the preferred method of control if a second heat source contributes heat to the zone.